Due to its non-reactivity as well as its tolerance for high temperatures, PTFE is also often used in industrial pipes and hose assemblies in which chemicals and acids are used.
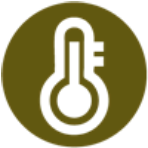
Polytetrafluoroethylene (PTFE) is also known as Teflon, a non-stick material frequently used in cookware and protective clothing. There are a host of industrial uses for this versatile material, too. PTFE is widely used in the aerospace, food and drink manufacturing, pharmaceuticals, and telecommunications sectors, to name but a few.
Pure PTFE is a low friction substance that can withstand huge changes in temperature, making it great for cookware such as non-stick pans. Physically, PTFE is highly flexible as well as extremely dense; therefore, a PTFE coating on machine parts makes them far more durable. Chemically, it is extremely unreactive and insoluble in most chemicals and is itself non-toxic, conferring further advantages in contexts such as laboratories, medicine (e.g. as a coating for catheters), and food manufacturing. Taken together, these properties make PTFE an extremely useful material for a wide range of applications across practically all industrial sectors
Because it is highly flexible, PTFE can creep and deform under heavy loads. This potential disadvantage can be obviated by adding a filler in order to benefit from the properties of both materials. Fillers can also add properties such as improved thermal conductivity, for applications that demand good heat dissipation. The most common filler material is glass, but other materials confer specific advantages for certain applications. These alternative additives include carbon, graphite, stainless steel, molybdenum disulfide, bronze, and polyimide.
“Virgin PTFE” (PTFE without a filler) is one of the most chemically inert materials known and is used in many different applications and industries.
Adding glass to PTFE makes it stronger and more durable, as well as reduces flexibility and the likelihood of creep. Glass-filled PTFE can operate at the same temperature range as virgin PTFE and is similarly chemically inert. Fluorotic offers Glass filled PTFE ranging from 5% to 60% glass content. Increasing the Glass filler content results in an increase in durability and compressive strength. Optionally, glass filled PTFE can be inert gas sintered. This further reduces the material’s tendency to creep as well as its porosity. Glass filled PTFE is more abrasive than Virgin PTFE, meaning that it can be abrasive to adjacent surfaces.
Carbon filled PTFE benefits from improved compressive strength, reduced deformation under heavy loads, and better wear resistance than virgin PTFE. Because carbon is conductive, it is suitable for applications which require higher thermal conductivity than PTFE alone and also becomes static dissipative due to its electrical conductivity. Carbon may be added in the form of powder or fiber. It can be abrasive, but not to the same extent as glass.
Graphite filled PTFE provides some similar benefits to ‘normal’ carbon filled PTFE but without the greatly improved wear resistance. Graphite lowers the coefficient of friction and Graphite filled PTFE has excellent self-lubricating properties. It can be combined with either carbon or glass or even both to reap the combined benefits of all three fillers.
If your application demands good thermal and electrical conductivity, bronze filled PTFE may be ideal. Adding bronze to PTFE also improves wear resistance. However, bronze attenuates the non-stick properties and chemical inertness of the PTFE, so you should consider whether these are important for your particular situation. Other metals such as titanium, nickel, or stainless steel (as described above) may also be chosen as fillers due to their specific properties.
Polytetrafluoroethylene (PTFE) is a synthetic fluoropolymer of tetrafluoroethylene.
Being hydrophobic, non-wetting, high density and resistant to high temperatures, PTFE is an incredibly versatile material with a wide variety of applications, though it’s perhaps best-known for its non-stick properties.
Due to its non-reactivity as well as its tolerance for high temperatures, PTFE is also often used in industrial pipes and hose assemblies in which chemicals and acids are used.
Due to its non-reactivity as well as its tolerance for high temperatures, PTFE is also often used in industrial pipes and hose assemblies in which chemicals and acids are used.
It’s low friction also makes it a popular material in mechanical engineering applications. It is regularly used for slide bearings, slide plates, gears and other working parts where sliding action takes place.
It is used frequently as an insulator for wiring and cable, particularly in computer applications, since it is an excellent electric insulator and has a high melting point.
PTFE is one of the most affordable fluoropolymers on the market, and has one of the best performances to price ratios.
It is often used in construction projects for structures such as car parks, supermarkets and bridges, since it enables affordable structure expansion without worrying about strain being put on rigid elements. Plus, its resistance against weather damage and general wear and tear make it an extremely long-lasting material.
Combined with its high temperature resistance PTFE is extremely chemically resistant and chemically inert making it an ideal material for sealing components in chemically aggressive applications.
This makes it an excellent choice for applications in food manufacturing and packaging, particularly since the material is food grade compliant and resistant to staining.